こんにちは、若手設計エンジニアのrickです!今回は、機械安全の世界で重要な資格「セーフティサブアセッサ」について、特に「リスクアセスメントのプロセス」に焦点を当ててお話しします。
皆さん、製品設計において安全性は最優先事項ですよね。でも、どうやって安全を確保すればいいのか悩んだことはありませんか?そんな時こそ、セーフティサブアセッサの出番です!
この資格は、機械安全の基礎知識とリスクアセスメントの実践力を証明するもので、設計エンジニアにとって非常に価値があります。安全な製品づくりはもちろん、法令遵守や顧客信頼の獲得にも直結するんです。
今日は、この資格の核心部分である「リスクアセスメントのプロセス」について詳しく解説していきます。
目次
参考書籍
日本認証株式会社 機械安全<初級>~リスクアセスメント実施者向け~
本記事の内容は、日本認証株式会社発行の「機械安全<初級>~リスクアセスメント実施者向け~」を参考にしています。
より詳細な情報をお求めの方は、ぜひこの書籍をご購入ください。機械安全とリスクアセスメントについて深く学べます。それでは本題に行きましょう!
リスクアセスメントの手順の概略
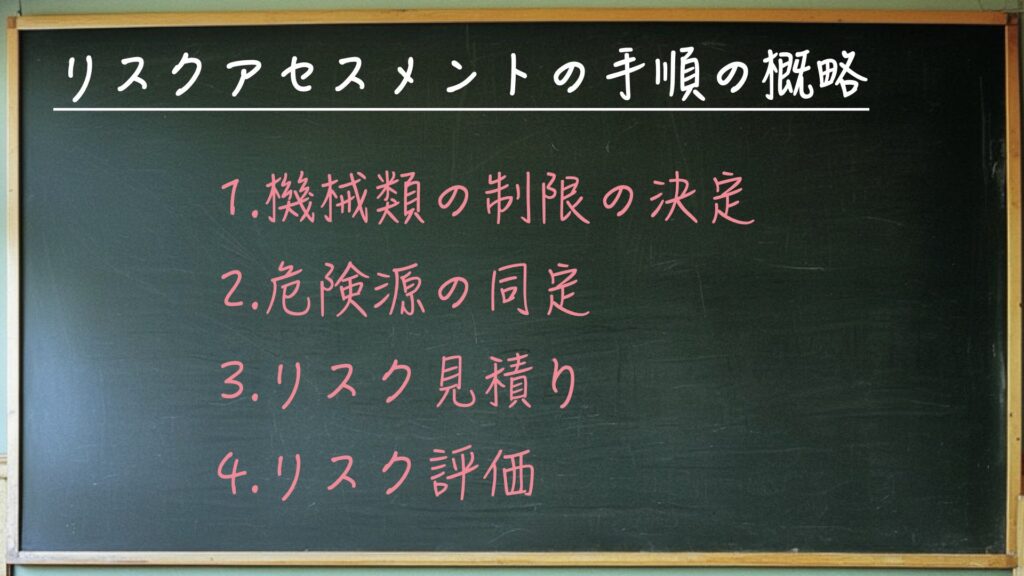
まずは全体の流れを把握しましょう。
リスクアセスメントは主に4つのステップで構成されています。
一つ目は機械類の制限の決定、二つ目は危険源の同定、三つ目はリスク見積り、そして最後にリスク評価を行います。
これらのステップを順番に進めることで、機械の安全性を総合的に評価し、必要な対策を講じることができるのです。
それでは、各ステップについて詳しく見ていきましょう。
1 機械類の制限の決定
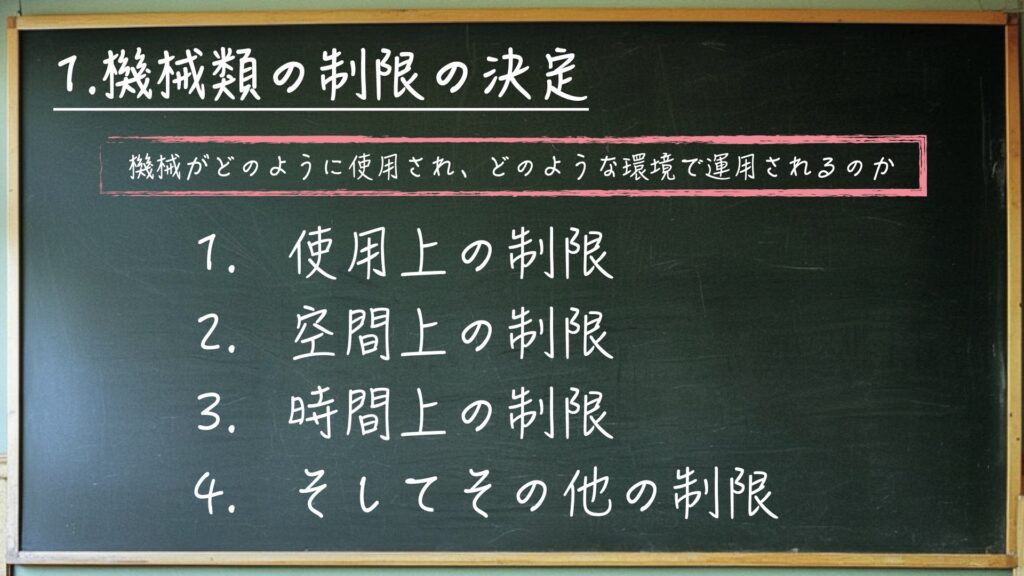
リスクアセスメントの第一歩は、機械類の制限を明確にすることです。
これは、機械がどのように使用され、どのような環境で運用されるのかを詳細に把握するプロセスです。具体的には、使用上の制限、空間上の制限、時間上の制限、そしてその他の制限の4つの観点から考えます。
これらの制限を正確に理解することで、後のステップでより的確な危険源の同定やリスク評価が可能になります。それでは、各制限について順番に見ていきましょう。
1-1 使用上の制限
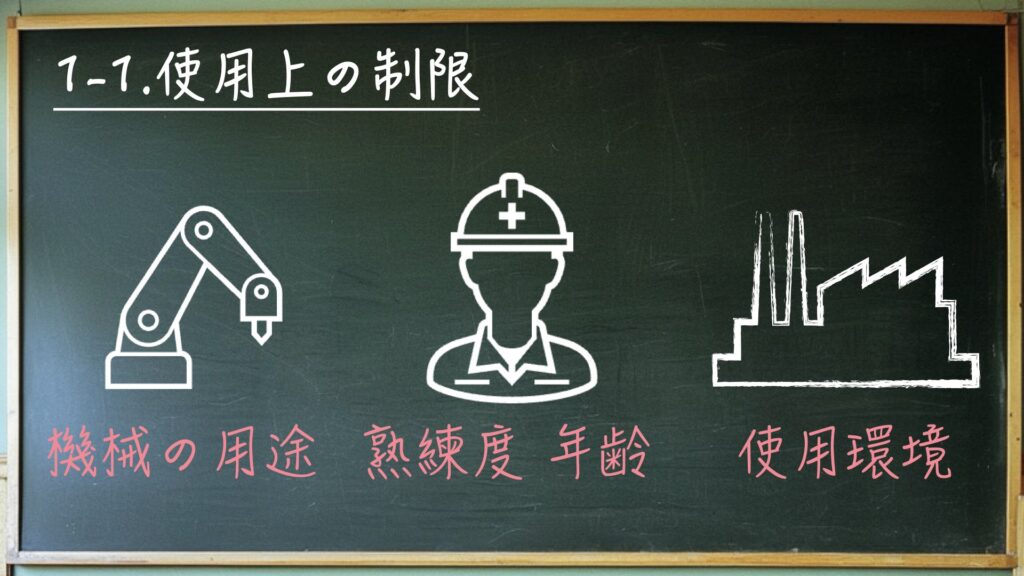
まず最初に、使用上の制限について説明します。これは、機械の意図された使用方法や予見可能な誤使用に関する制限のことです。
例えば、機械の用途、使用者の特性(熟練度、年齢など)、使用環境(屋内・屋外、温度、湿度など)が含まれます。また、機械の運転モード(自動、手動、メンテナンスモードなど)も考慮します。
これらの情報を明確にすることで、機械が使用される際に発生しうる危険状況を予測しやすくなります。
1-2 空間上の制限
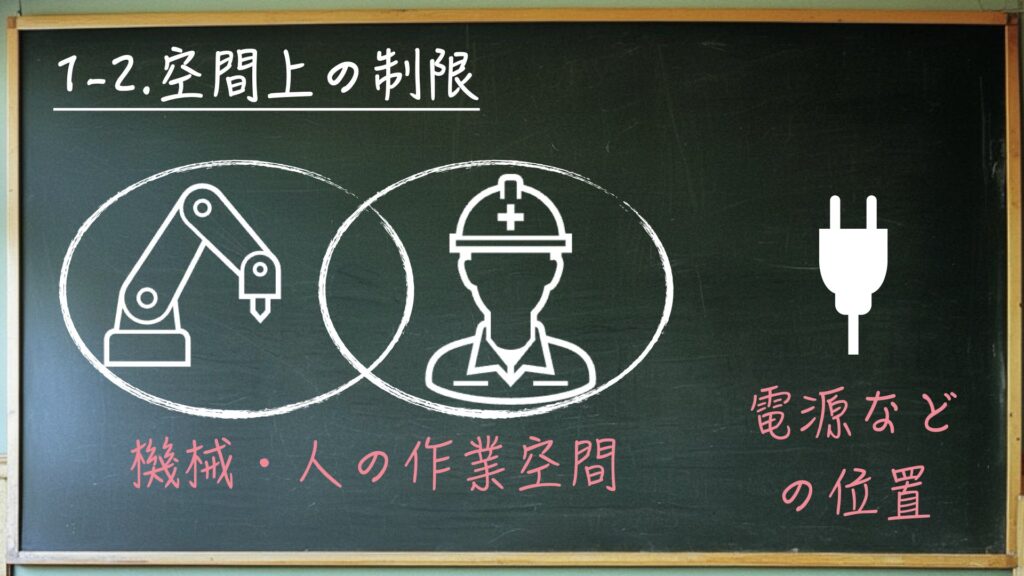
次に、空間上の制限について見ていきましょう。
これは、機械の動作範囲や設置場所に関する制限を指します。具体的には、機械の寸法、必要な作業空間、人と機械の相互作用が行われる範囲などが含まれます。また、機械の設置に必要なユーティリティ(電源、圧縮空気など)の位置や、メンテナンス時のアクセス空間なども考慮します。
これらの制限を明確にすることで、機械の周囲で発生しうる危険状況を特定しやすくなります。
1-3 時間上の制限
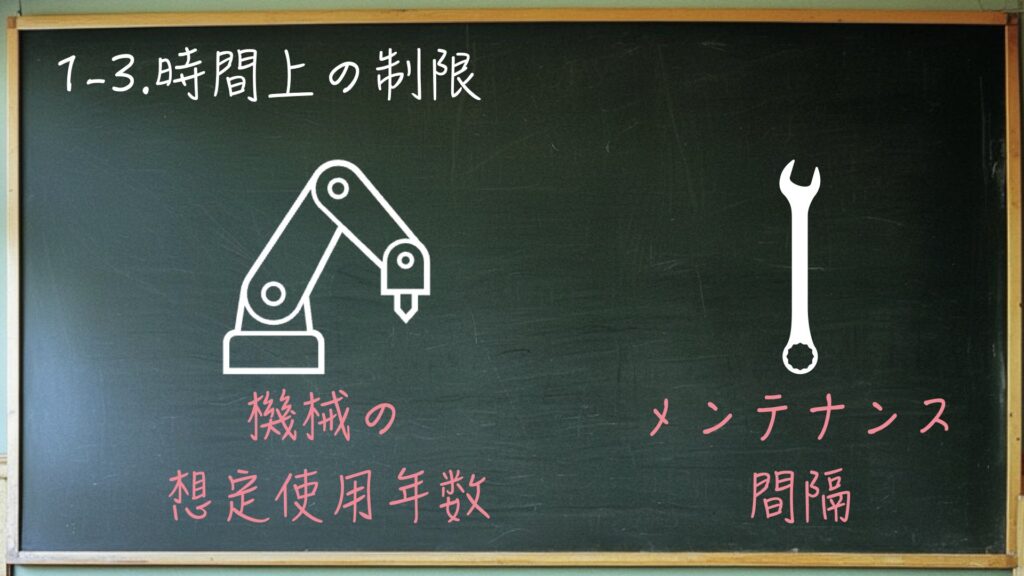
続いて、時間上の制限について説明します。これは、機械の寿命や使用頻度に関する制限を指します。
例えば、機械の想定使用年数、部品の交換周期、メンテナンス間隔などが含まれます。また、機械の運転サイクル(連続運転か間欠運転か)や、季節による使用頻度の変化なども考慮します。これらの情報は、機械の劣化や疲労による危険源を予測する上で重要です。
時間上の制限を正確に把握することで、長期的な安全性を確保し、適切なメンテナンス計画を立てることができます。
1-4 その他の制限

最後に、その他の制限について見ていきましょう。こ
れには、上記の3つのカテゴリーに当てはまらない様々な制限が含まれます。例えば、加工する材料の特性(硬さ、腐食性など)、清掃や廃棄物処理に関する制限、法規制による制限などが挙げられます。また、機械の運用に必要な特殊な訓練や資格なども、ここで考慮します。
これらの制限を漏れなく把握することで、より包括的なリスクアセスメントが可能になります。
2 危険源の同定
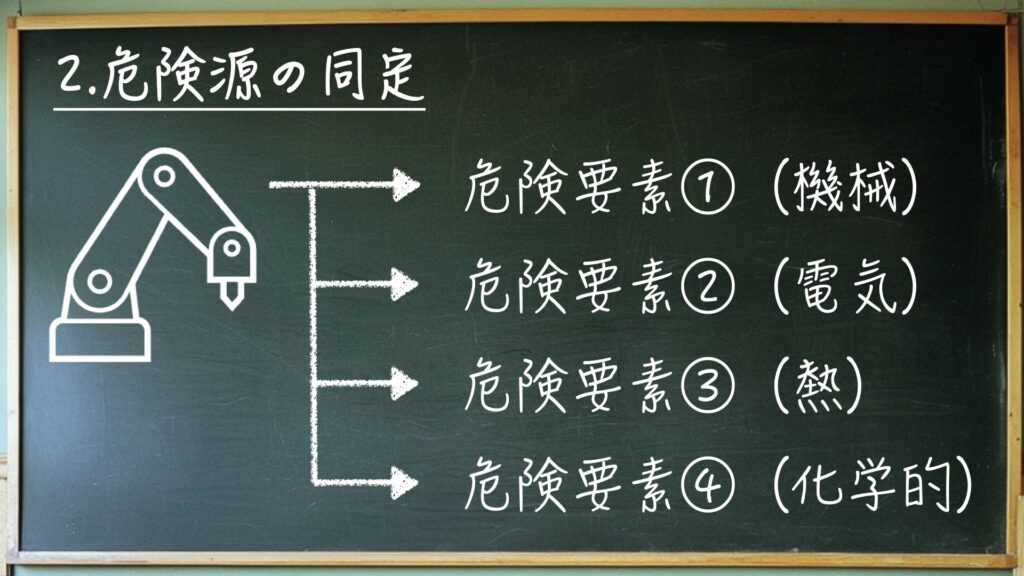
機械類の制限を決定したら、次は危険源の同定に移ります。
これは、機械に潜む潜在的な危険を特定するプロセスです。ここでは、機械の設計図面や実機を詳細に調査し、人体に危害を与える可能性のあるすべての要素を洗い出します。
危険源は、機械的なものだけでなく、電気的、熱的、化学的なものなど、多岐にわたります。また、通常の使用時だけでなく、予見可能な誤使用やメンテナンス時の危険源も考慮する必要があります。
2-1 危険源の種類
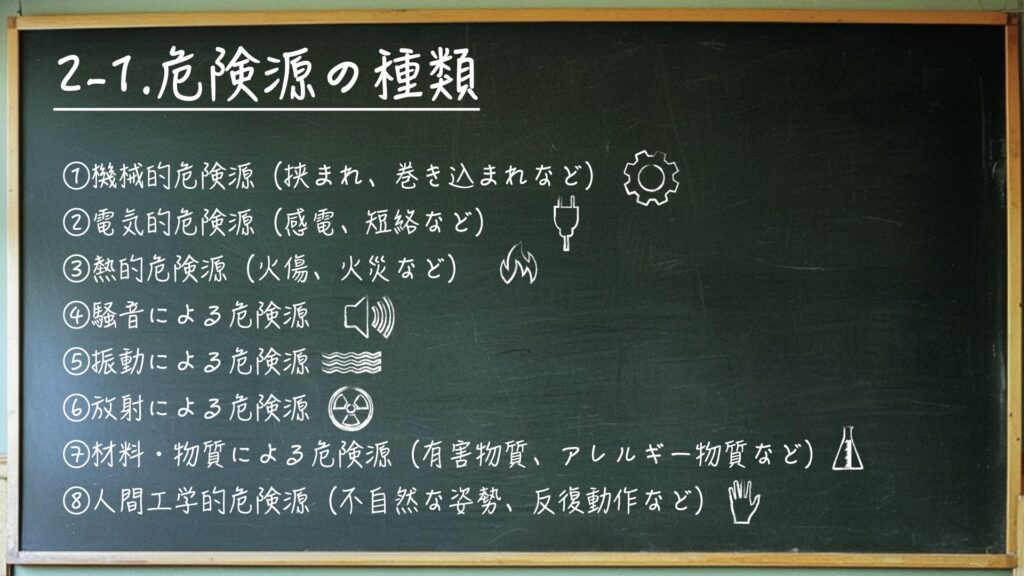
危険源には様々な種類があります。
主なものとして、
- 機械的危険源(挟まれ、巻き込まれなど)
- 電気的危険源(感電、短絡など)
- 熱的危険源(火傷、火災など)
- 騒音による危険源
- 振動による危険源
- 放射による危険源
- 材料・物質による危険源(有害物質、アレルギー物質など)
- 人間工学的危険源(不自然な姿勢、反復動作など)
があります。
これらの危険源を漏れなく特定することが、効果的なリスクアセスメントの鍵となります。
3 リスク見積もり
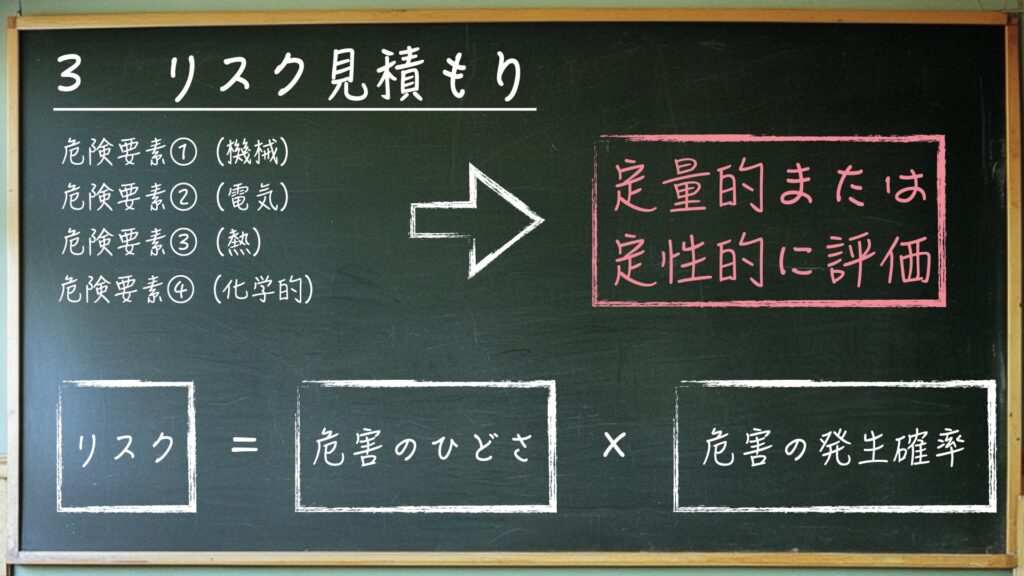
危険源を特定したら、次はリスク見積もりに進みます。
これは、特定された各危険源について、その危険性の程度を定量的または定性的に評価するプロセスです。ここでは主に二つの要素、「危害のひどさ」と「危害の発生確率」を考慮します。これらの要素を組み合わせることで、各危険源のリスクレベルを決定します。
リスク見積もりは、後のリスク評価や対策の優先順位付けの基礎となる重要なステップです。
3-1 危害のひどさ
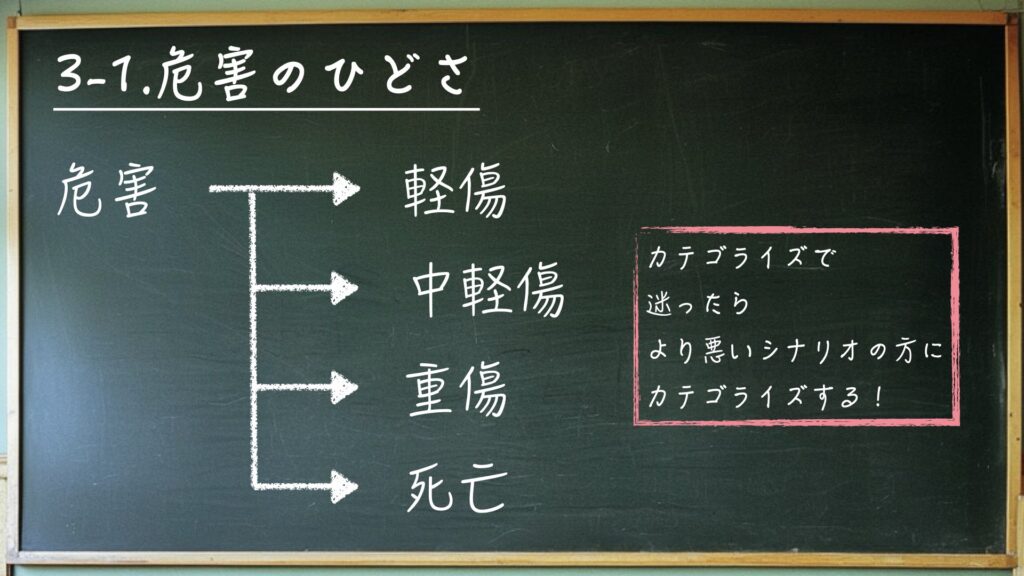
リスク見積もりの一つ目の要素は、危害のひどさです。
これは、危険源によって引き起こされる可能性のある傷害や健康障害の重大性を評価します。一般的に、軽傷、重傷、死亡などのカテゴリーに分類されます。
評価の際は、最悪のシナリオを想定することが重要です。また、一度に複数の人が被害を受ける可能性や、長期的な健康影響なども考慮します。
危害のひどさを正確に評価することで、より適切なリスク対策を講じることができます。
3-2 危害の発生確率
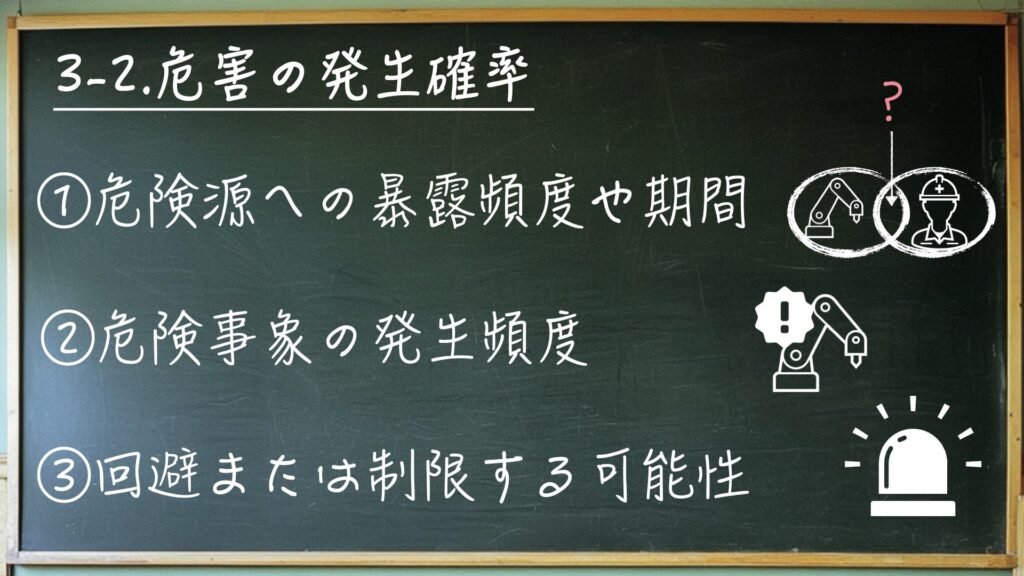
リスク見積もりの二つ目の要素は、危害の発生確率です。
これは、危険事象が実際に起こる可能性を評価します。評価には、危険源への暴露頻度や期間、危険事象の発生頻度、危険を回避または制限する可能性などが含まれます。
過去の事故データや類似機械の統計、専門家の意見などが活用されます。また、人的要因(操作者の熟練度、疲労など)や環境要因(照明、温度など)も考慮します。
発生確率を適切に見積もることで、リスクの現実的な評価が可能になります。
4 リスク評価
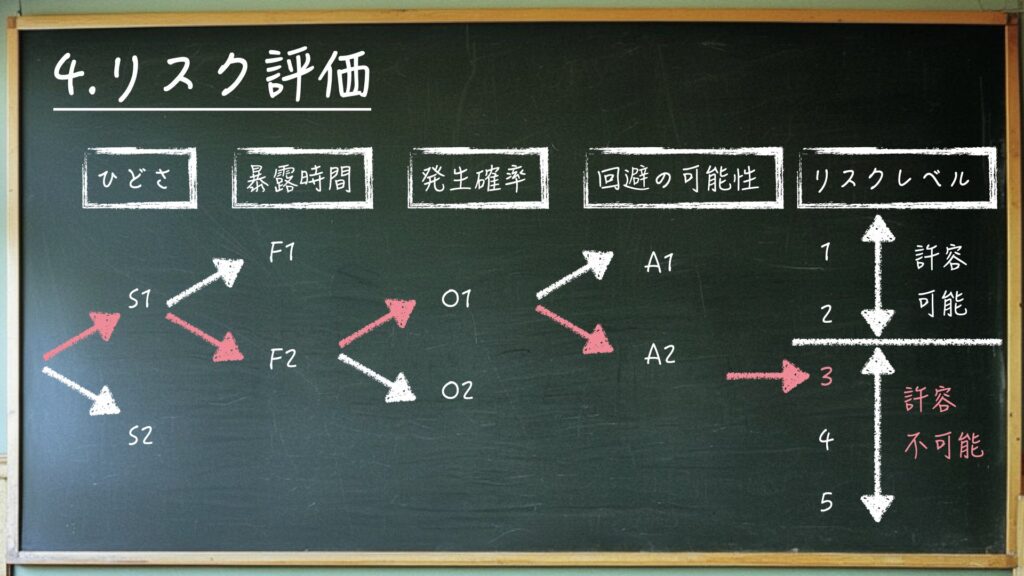
最後のステップは、リスク評価です。
これは、リスク見積もりの結果を基に、そのリスクが許容可能かどうかを判断するプロセスです。ここでは、見積もられたリスクレベルと、予め設定された許容可能なリスクレベルを比較します。
許容できないと判断されたリスクについては、リスク低減措置を検討する必要があります。評価の際は、法規制や業界標準、企業の安全方針なども考慮します。
リスク評価の結果は、機械の設計変更や安全対策の実施、使用上の注意事項の策定などに直接反映されます。
最後に
いかがでしたか?リスクアセスメントのプロセスについて、詳しく解説してきました。
このプロセスを理解し、実践することで、機械の安全性を大幅に向上させることができます。セーフティサブアセッサとして、これらの知識は非常に重要です。
今回の内容をしっかり復習して、実際の機械設計や安全管理に活かしてください。安全な機械設計は、作業者の安全を守るだけでなく、企業の信頼性向上にも大きく貢献します。次回の記事では、リスク低減措置の具体的な方法について詳しく解説する予定です。
これからも一緒に勉強を頑張っていきましょう!安全な社会の実現に向けて、私たちの知識と技能を磨き続けていきましょう。それでは、次回の記事でまたお会いしましょう!
ブログの内容を動画でも解説しています!YouTubeもぜひチェックして、学びを深めましょう!