こんにちは、若手設計エンジニアのrickです!今日は、私の経験を活かして、セーフティサブアセッサの資格取得を目指す方々に向けて、重要なキーワードをご紹介したいと思います。
皆さん、機械安全って聞いたことありますか?近年、産業現場での安全性向上が急務となっており、セーフティサブアセッサの資格がますます注目されています。この資格は、国際安全規格に基づく機械安全の知識を認証するもので、私自身、生産技術者としての成長に大きく貢献してくれました。
セーフティサブアセッサは、安全な製品設計や作業環境の構築に不可欠な知識を身につけられる素晴らしい機会です。資格取得により、自身のキャリアアップはもちろん、職場全体の安全文化向上にも貢献できるんです。
目次
参考書籍
日本認証株式会社 機械安全<初級>~リスクアセスメント実施者向け~
本記事の内容は、日本認証株式会社発行の「機械安全<初級>~リスクアセスメント実施者向け~」を参考にしています。
より詳細な情報をお求めの方は、ぜひこの書籍をご購入ください。機械安全とリスクアセスメントについて深く学べます。それでは本題に行きましょう!
機械安全の基礎とは

セーフティサブアセッサの「機械安全の基礎」では、
①主な危険源の種類とその概要として、機械的、電気的、熱的、騒音、振動などの危険源を学びます
また、
②リスクアセスメント及びリスク低減のための方法論として、ISO 12100に基づく機械の制限の指定、危険源の同定、リスクの見積り・評価、保護方策の検討・実施を学習します。
主な危険源の分類
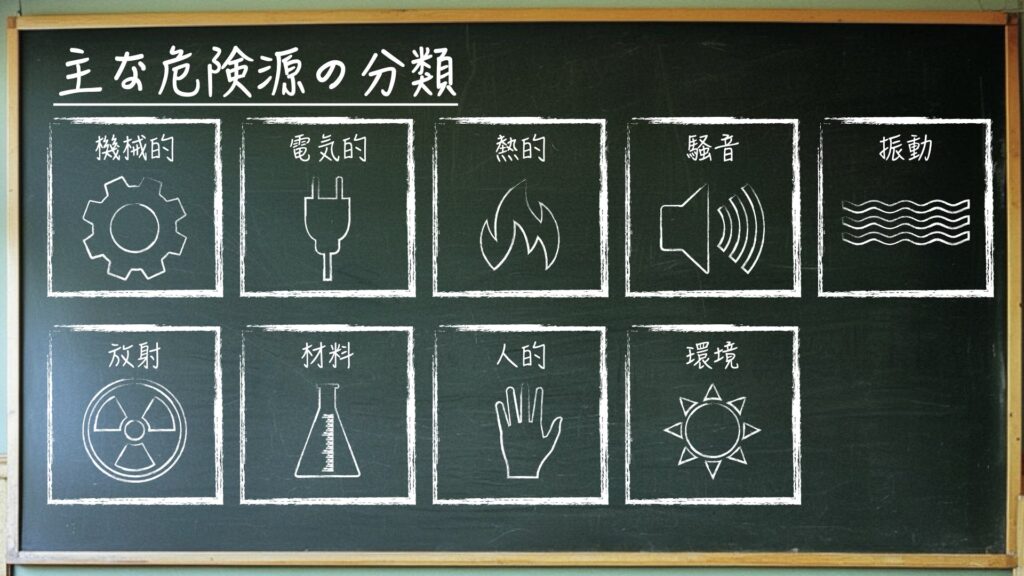
はじめに主な危険源の分類について説明します。
主な危険源の種類は、 以下の9つに分けられます。 機械的危険源、電気的危険限、熱的危険限、騒音による危険限、振動による危険限、放射による危険源、材料及び物質による危険、人的要因、環境要因です。 これら一つ一つの危険源について、次のスライドから説明していきます。
①機械的危険源
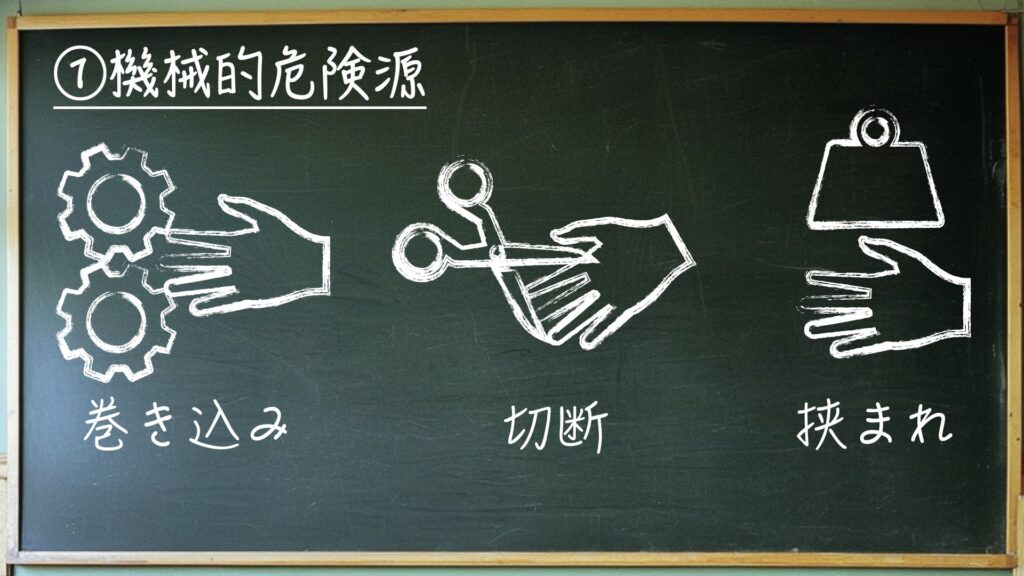
1つ目は機械的危険源です。
機械的危険源は、可動部品や回転要素によって引き起こされる危険です。例えば、回転するシャフトやベルトによる巻き込みや切断のリスクがあります。また、挟まれ事故も多く発生しており、特に設計段階での安全対策が重要です。適切なガードやインターロック装置の設置が求められます。
②電気的危険源
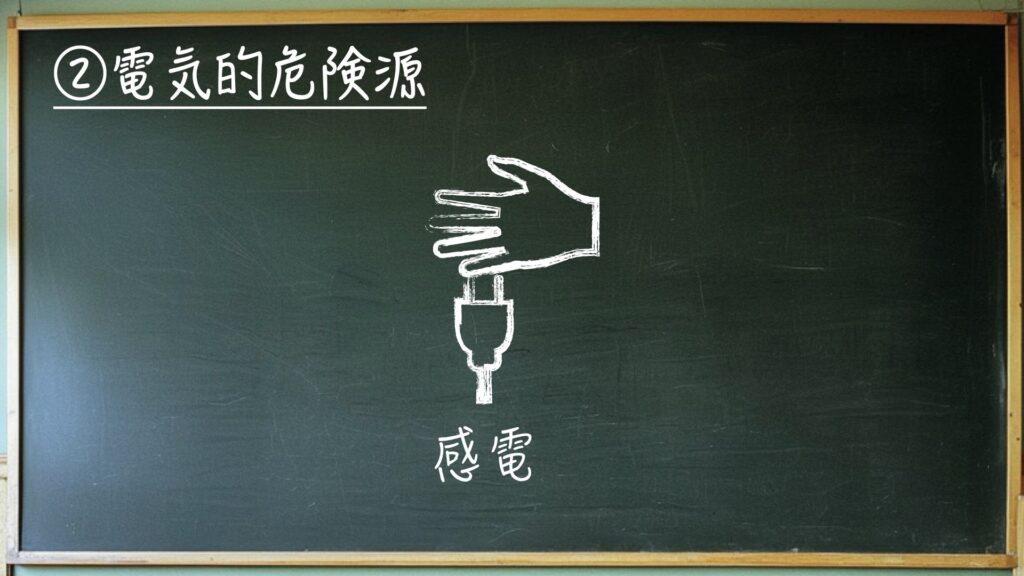
電気的危険源は、電気設備や配線に関連するリスクです。漏電やショートによる感電や火災が主な問題です。特に湿気の多い環境では、電気機器の故障が発生しやすくなります。適切な絶縁処理や定期的な点検を行うことで、安全性を向上させることができます。
③熱的危険源
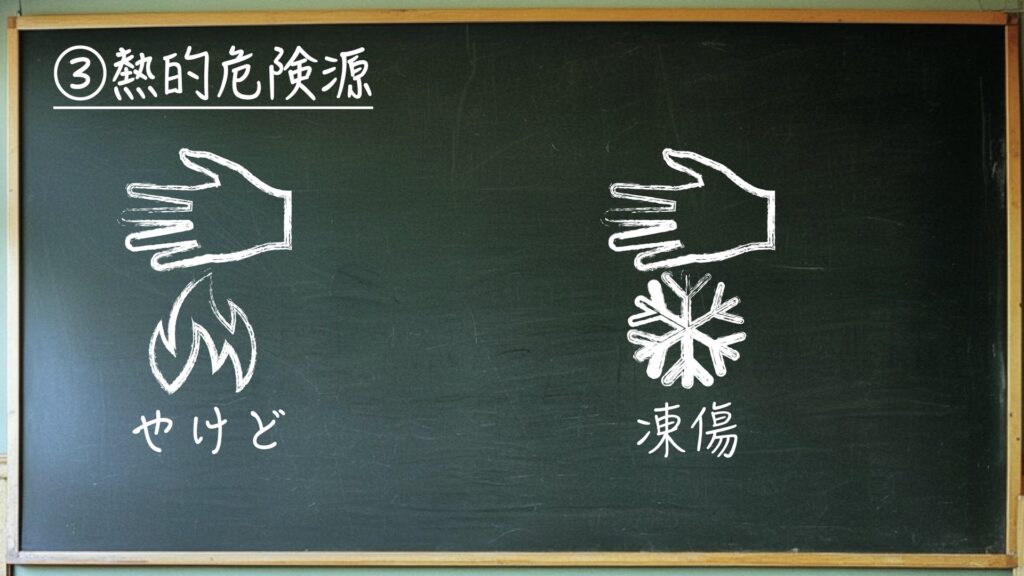
3つ目は熱的危険源です。
熱的危険源は、高温または低温によるリスクを指します。高温にさらされることで火傷や火災が発生する可能性があります。一方で、低温環境では凍傷などの健康被害が懸念されます。作業者には適切な防護具を提供し、安全な作業環境を維持することが重要です。
④騒音による危険源
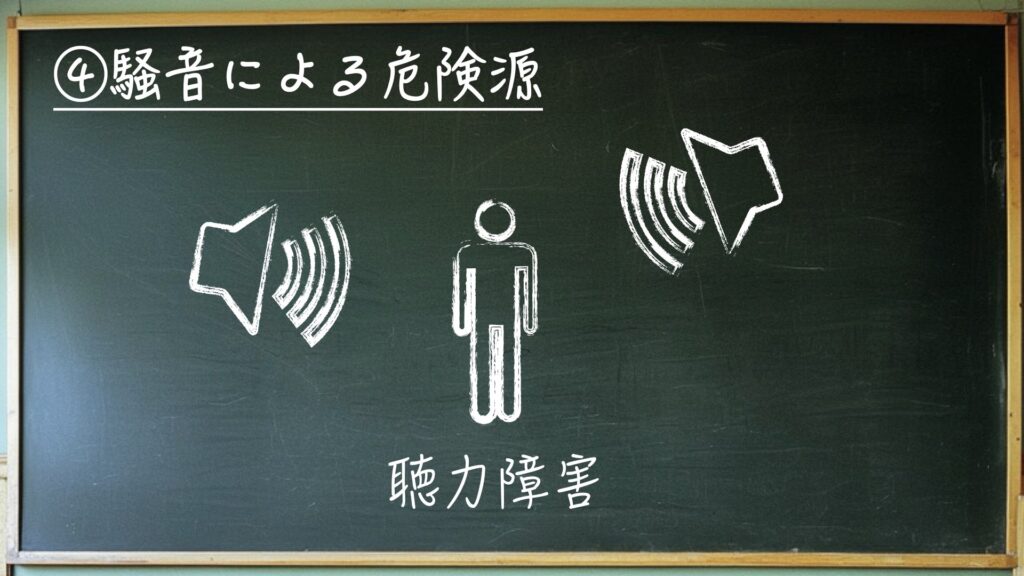
4つ目は騒音による危険源です。
騒音は作業環境において見落とされがちな危険源ですが、長時間の曝露は聴力障害を引き起こす可能性があります。特に工場などの騒音が大きい場所では、耳栓などの防護具を使用することが推奨されます。また、騒音レベルを測定し、必要に応じて防音対策を講じることも重要です。
⑤振動による危険源
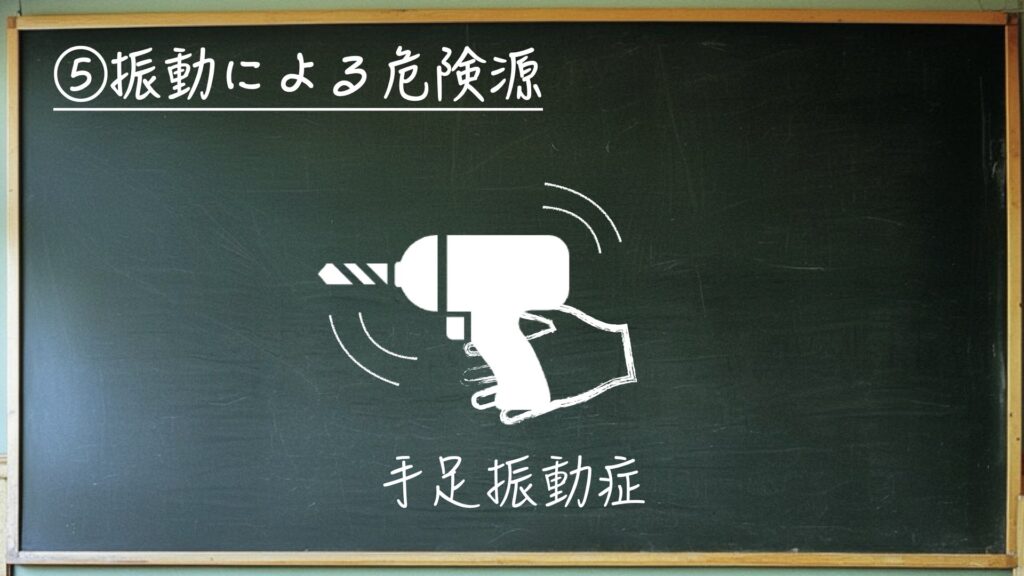
5つ目は振動による危険源です。
振動は機械操作中に発生し、長時間曝露されると健康に悪影響を及ぼす可能性があります。手足振動症(HAVS)などの疾患が代表例であり、特に手持ち工具を使用する作業者には注意が必要です。振動対策としては、振動吸収マットや適切な作業姿勢が効果的です。
⑥放射による危険源
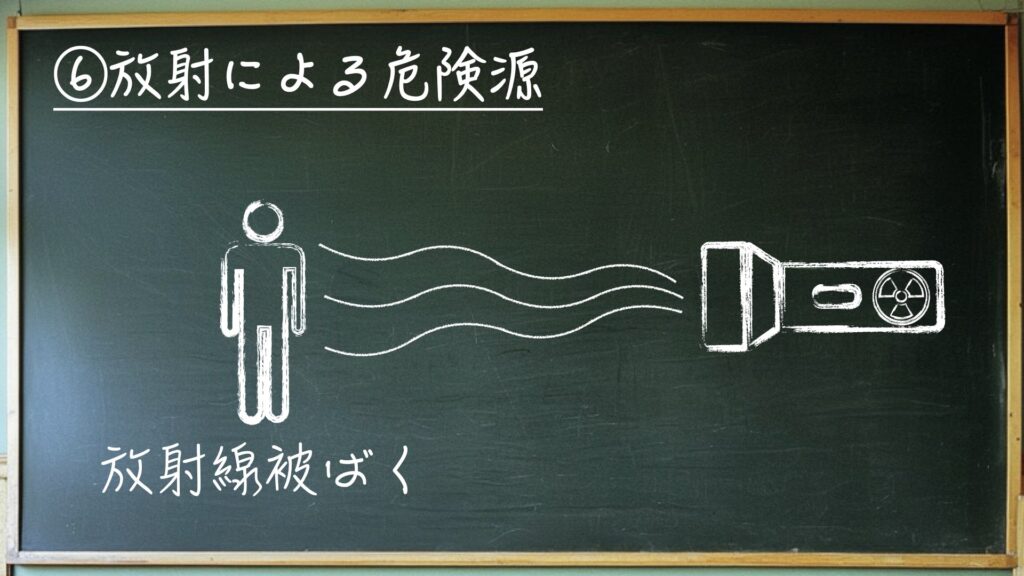
6つ目は放射による危険源です。
放射線は特定の業界で問題となる危険源であり、特に医療や研究分野で注意が必要です。放射線による健康被害(癌など)を防ぐためには、防護壁やシールド材の使用が求められます。また、放射線量のモニタリングも重要な対策です。
⑦材料及び物質による危険
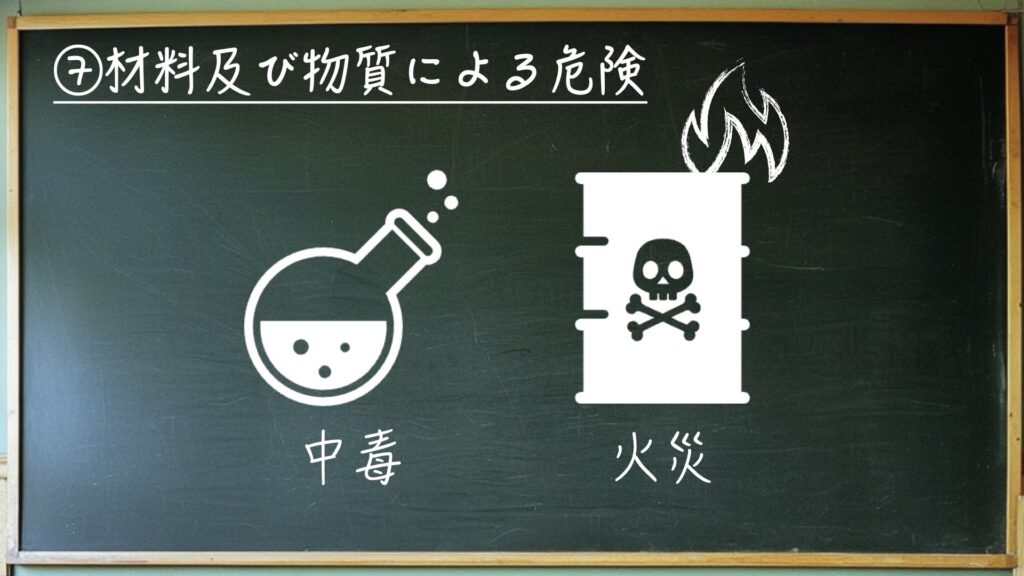
7つ目は材料及び物質による危険です。
化学物質や有害物質は、中毒や火災の原因となります。特に取り扱い時には注意が必要で、安全データシート(SDS)を確認しながら適切な防護具を使用することが重要です。また、有害物質の取り扱いには訓練されたスタッフによる管理も欠かせません。
⑧人的要因
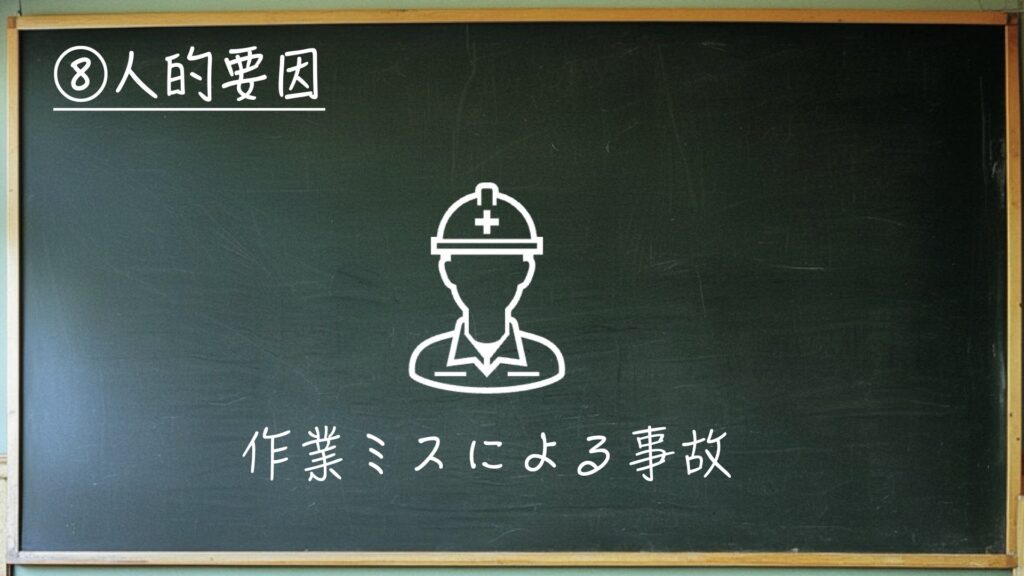
8つ目は人的要因です。
人的要因は、多くの場合事故の主な原因となります。操作ミスや不適切な教育によって引き起こされる事故は非常に多く、新入社員や未経験者には十分な教育と訓練が求められます。また、ストレスや疲労も人的要因として考慮しなければならないポイントです。
リスクアセスメント及びリスク低減のための方法論

次にリスクアセスメント及びリスク低減の方法論について説明します
リスク低減におけるステップとしては、初めにリスクアセスメントを行い、危険源のリスク評価を行います。
次に3ステップメソッドによるリスク低減を行います。
具体的なステップとしては、ステップ1で本質的安全設計方策を、ステップ2で安全防護及び保護方策を、ステップ3で使用上の情報をそれぞれ検討していきます。 つぎに使用者によって講じられる保護方策によって残留リスクをなくしていきますが、低減しきれないリスクについては再びリスクアセスメントから行います。
具体的な内容については次のスライドから説明していきます。
リスクアセスメント
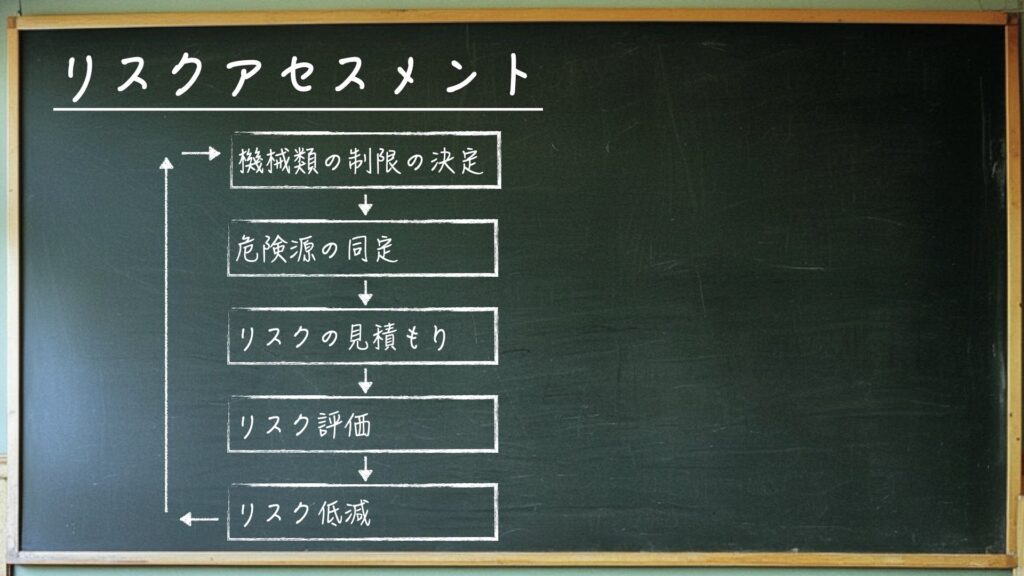
初めにリスクアセスメントについて説明します。
リスクアセスメントは、機械が持つ危険源を特定し、それに伴うリスクを評価するプロセスです。
ISO 12100では、以下の手順が推奨されています。
「機械類の制限の決定」では対象となる機械やシステムの範囲を明確にします。
「危険源の同定」では機械が持つ潜在的な危険源を特定します。
「リスクの見積り」では危険源が引き起こす可能性のある危害の程度と発生確率を評価します。
「リスク評価」では見積もったリスクが許容可能かどうかを判断します。
「リスク低減策の選定」では許容できないリスクについて、適切な低減策を講じます。
①本質的安全設計方策
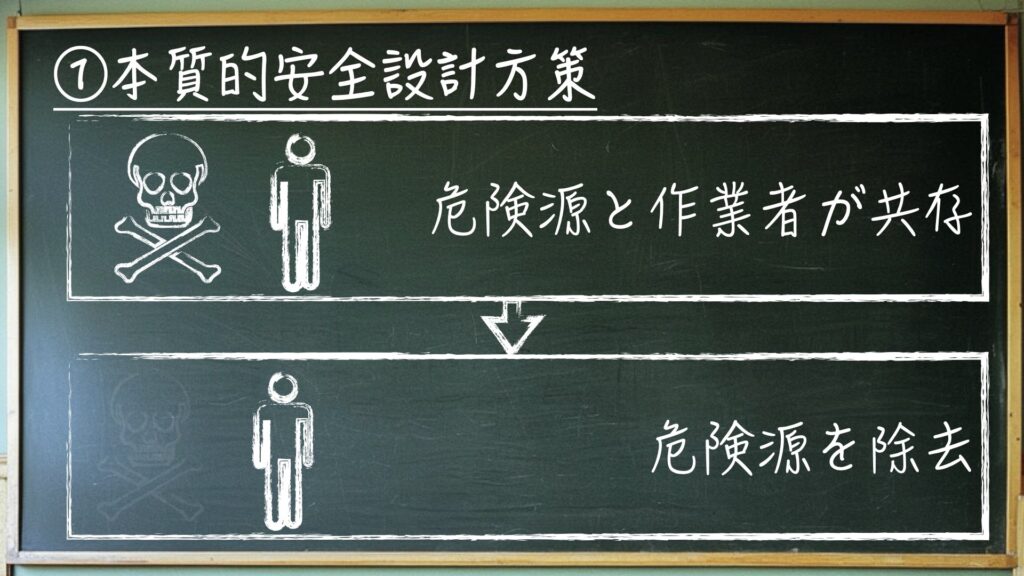
つぎに本質的安全設計方策についてです。
本質的安全設計は、危険源そのものを排除または削減することに焦点を当てています。具体的には以下のような方法があります。
①危険動作部分の除去
②作業環境の変更(例:高所作業から低所作業への変更)
③自動化による人間の暴露機会の削減
この段階で新たな危険源が生じないよう十分な配慮が必要です。
②安全防護及び付加保護方策
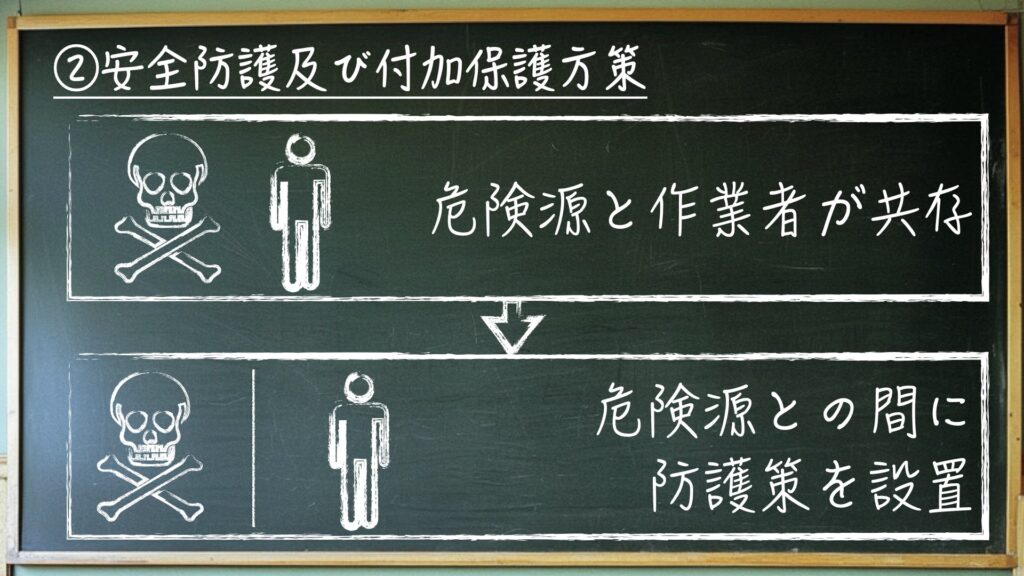
次に安全防護及び付加保護方策についてです。
安全防護方策は、物理的な障壁や検知装置によって危険から守る方法です。
具体例としては
①固定式ガード
②インターロック付き可動式ガード
③検知保護設備(セーフティマットなど)
付加保護方策には、非常停止装置や警報システムなどが含まれ、これらは緊急時に迅速に対応できるよう設計されています。
③使用上の注意
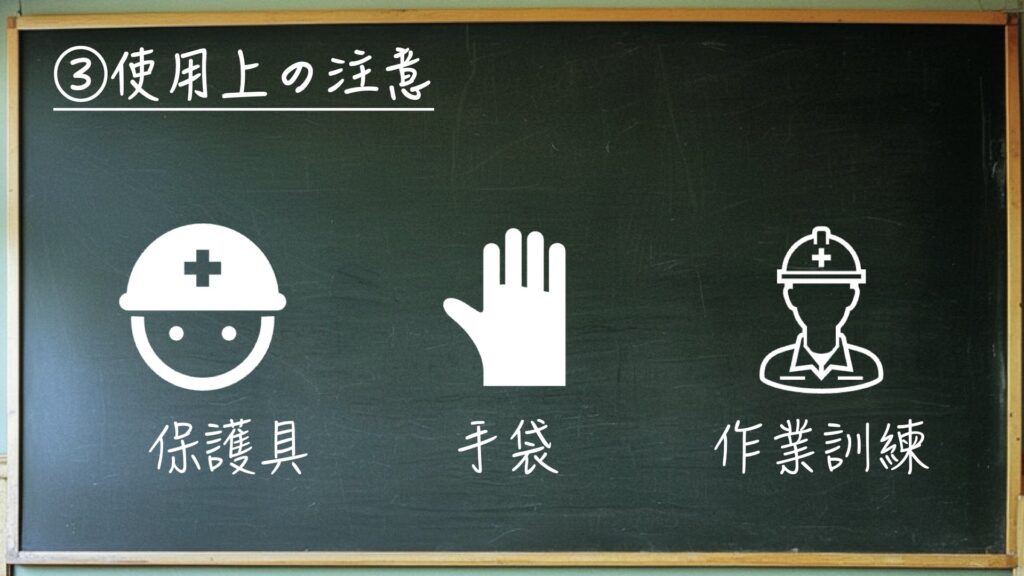
次に使用上の注意についてです。
使用上の注意は、安全な作業手順や残留リスクについて使用者に通知するために重要です。
具体的には
①使用説明書やラベルで残留リスクや必要な保護具について明示する
②視聴覚信号による警報システムを導入する。
使用者もまた、自身や周囲の安全を守るために以下のような対策を講じることが求められます。
①保護具(ヘルメット、安全靴など)の着用
②機械操作前の訓練受講
③定期的なメンテナンスと点検。
これらは設計者による防護方策と相互補完的であり、安全文化の醸成にも寄与します。
最後に
皆さん、いかがでしたか?セーフティサブアセッサの基礎知識について、一緒に学んでいきましたね。機械安全は奥が深く、常に新しい技術や規格が登場する分野です。この記事で紹介した内容は、あくまでも入り口に過ぎません。これからも一緒に勉強を続けていきましょう。
次回の記事では、より具体的な事例を交えながら、機械安全規格における安全の概念について詳しく解説していく予定です。安全な職場づくりは、私たち一人一人の意識と行動から始まります。これからも共に成長し、より安全で効率的な作業環境の実現を目指しましょう。次の記事でまたお会いできることを楽しみにしています!
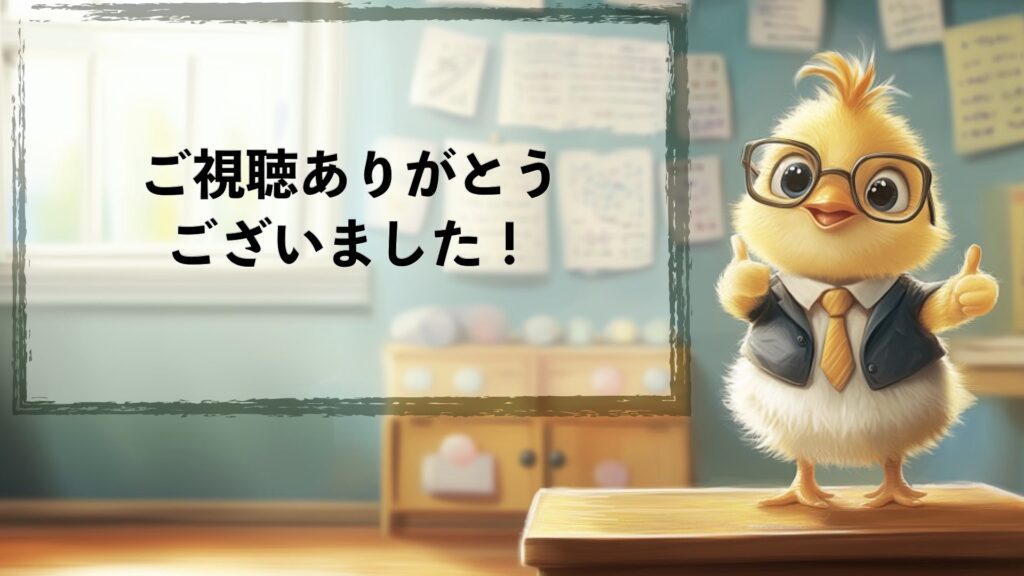